What Are the Steps of Sheet Metal Box Machining?
With the continuous development of modern society, the sheet metal shell processing industry has also been developed rapidly. For any sheet metal parts, there are certain processing steps. The sheet metal shell processing steps are the pivotal technology that the sheet metal technical staff needs to grasp, and it is also an important process for forming sheet metal products. So do you know how the steps of sheet metal shell processing are like? The following is a brief introduction by JIATONG XJ sheet metal supplier
Steps of Machining Custom Sheet Metal Boxes:
1. Drawing design.
Generally customers provide drawings or samples, the company’s engineering staff to measure, design, unfold, the formation of sheet metal shell processing decomposition and assembly diagram submitted to the production department processing.
2. Laser processing.
Laser cutting machine can be used to cut materials such as carbon steel, stainless steel, etc. Using laser cutting, the workpiece is processed with neat, smooth and beautiful cross-section, accurate size, and more advantageous for workpieces with arcs, which is the processing method of sheet metal shells that cannot be replaced by general CNC stamping.
3. CNC stamping.
Turret CNC punching machine is mainly for products processed with thin material thickness, generally more suitable for materials below 2.5mm, sheet metal shell processing workpieces with more holes or workpieces that need to open special molds to be processed, and when the batch is larger, using CNC punching has certain cost advantages.
4. Bending.
After the workpiece is well material such as most need to bending molding, the company has more than one computer bending machine, not only fast, sheet metal shell processing more accurate.
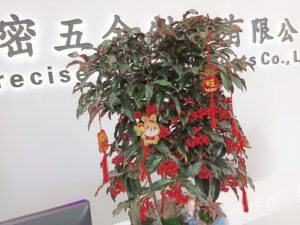
5. Welding forming.
Workpieces in the next good material generally need to be assembled into shape, there are a variety of ways to assemble, some directly with screws, riveting and other non-welding process molding, general mechanical shell of the sheet metal shell more use welding molding, the company generally take argon arc welding, touch welding, carbon dioxide welding, etc., after welding the workpiece polishing polishing, so that the workpiece is more solid, beautiful.
6. Electrostatic powder spraying.
Electrostatic powder spraying is mainly for carbon steel workpiece, in the sheet metal shell processing process is generally first oil and rust removal, table conditioning cleaning, phosphate treatment, electrostatic powder spraying, high-temperature baking and other processes, after treatment of the workpiece surface beautiful, several years will not rust, low cost and other advantages. Liquid paint this process is different from electrostatic powder spraying, generally for large workpieces, in the case of the inability to transport the use of liquid paint has the advantage of convenience, low cost, etc. Liquid paint is generally divided into two steps, in the workpiece after treatment on the primer and then top coat.
7. Packaging for shipment.
100% inspection before packing, and provide inspection data. The shipment requirements and packaging methods are confirmed by the customer’s representative on the spot, which is hereby recorded for the customer to confirm again.
In summary, these are the steps of sheet metal shell processing. Each step of sheet metal shell processing is very important, and any problem in one step will affect the processing quality of the product. Therefore, each step of the sheet metal shell processing process should be done well so that we can make sheet metal shell products with qualified quality. Click here to inquire more details about custom metal boxes, custom aluminum box from JIATONG XJ custom metal box manufacturers.